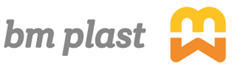
B. M. Plast d.o.o. was established in 2002 as a family-owned plastic processing company.
More than 50% of the company´s income is generated on the EU market.
The director, Mr. Mate Babić, has been working in the field of plastic processing for over 35 years, during which he has encountered different ways of processing plastics: injection moulding, blowing, roll casting, extrusion and injection blow moulding.
Currently the company is using the following technologies:
- injection moulding for various packaging products, assembly parts, machine parts, technical semi-finished products, as well as finished assemblies
- IBM (injection blow moulding) for bottles of different shapes and volumes (from 5 ml to 700 ml).
In production, in addition to classic materials (PP, PE, PS), also products and assemblies from technical materials (ABS, PA, POM, PC) are made.
In recent years, the company has been more focused on pharmaceutical products (bottles for nose and eye drops of different volumes).
The products are made in a class C cleanroom and afterwards sterilized in cooperation with Mediscan GmbH – Austria (E-Beam technology) or the Ruđer Bošković Institute (Gamma radiation). The company owns various injection moulding and injection blow moulding (IBM) machines with a closing force of 500 to 3.500 KN and an injection volume of up to 1.060 cm3 (950 g – max weight of the injected piece). There is also a machine for high frequency welding of plastics (blisters).
Since the company is committed to sustainability, it is currently working on the development of pocket packaging for disinfectants made of biodegradable materials.
In the past, the company has supported as technical partner two projects of the Center for Biomodelling and Innovation in Medicine of the Faculty of Medicine in Rijeka, Croatia:
In 2018 the construction of an innovative aid for disabled persons (walking stick with GPS, USB-slot and light)
In 2020 the construction of visors made of biodegradable material, regarding the recent COVID-19 pandemic. This project is still ongoing. A substantial part of both projects is 3D printing, as the products are printed out first to be tested for their functionality.
In general, the company uses in recent years 3D printing for developing new products, as this is much faster and cheaper than making pilot moulds for testing.
We are confident, that we can with our expertise and experience in plastic processing contribute to the BRIGHT project. This would be the first time the company is participating in an EU funded project.